A world of
magnificent patterns
Ita are a kind of flat carved wooden platter that is a part of inherited Ainu culture. Nibutani Ita, the style particular to the Saru River basin where Nibutani, Biratori stands, is an officially designated Traditional Craft Product.
These implements have a very long history as food servers in daily life, while half-moon and round shaped ita trays were presented to the Shogunate rulers at the end of the Edo period (1603-1867).
In the following Meiji period (1868-1912), master craftsmen began to produce and sell ita and other small items carved with patterns unique to this region. Their tried and true techniques have been handed down to modern artisans.
The wood used is mostly Japanese Katsura tree (Cercidiphyllum japonicum) and walnut, and most are decorated with arrangements of the key Ainu patterns of morew-noka, ay-us-noka, and sik-noka, with the scale-patterns of ramram-noka filling the gaps between, a characteristic of the region.
Production processes
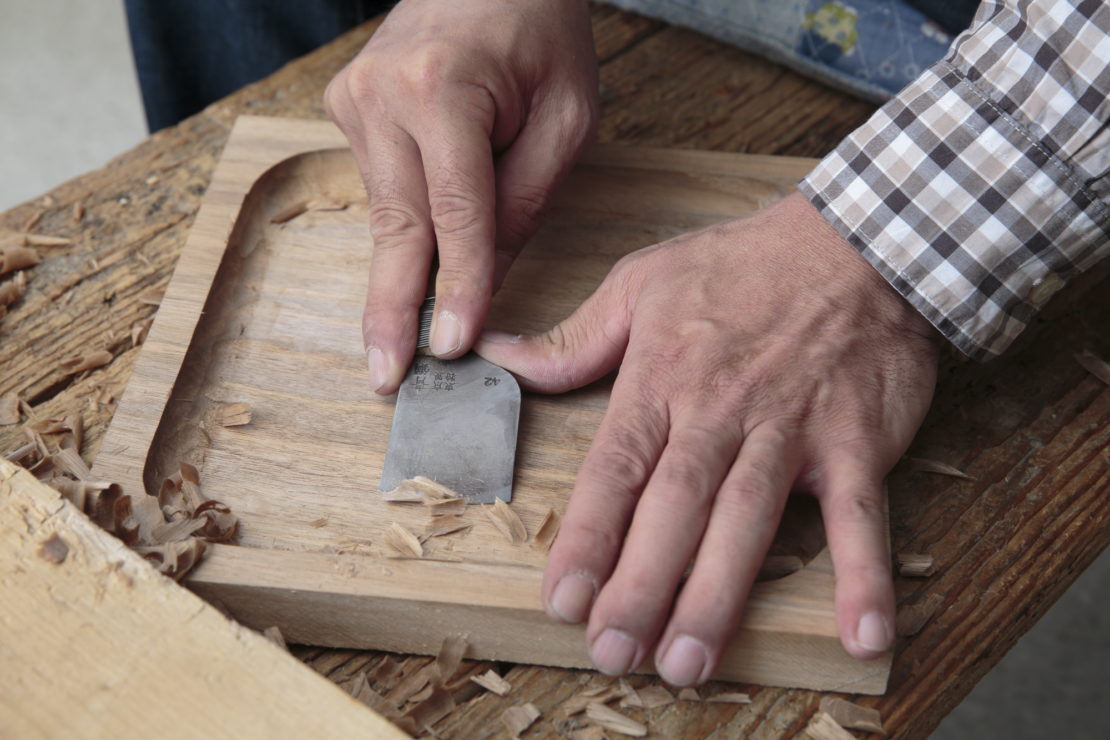
1. Bottoming
With a leather cutting knife, the carver hollows out the interior of a rough-hewn board to a uniform depth.
The interior lines are carefully finished using a gouge.
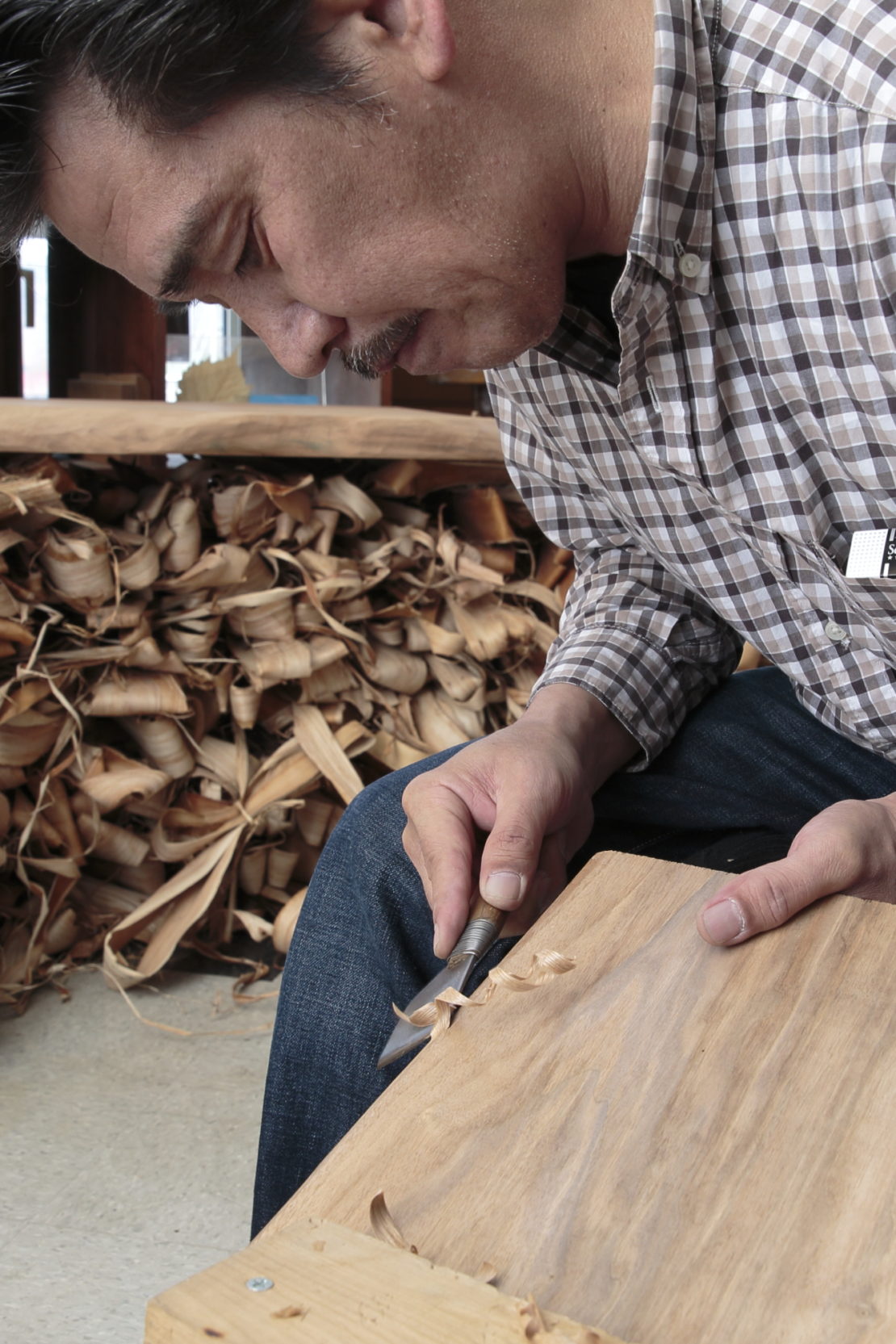
2. Reverse finishing
The back corners are chamfered,
finishing the ita’s shape.
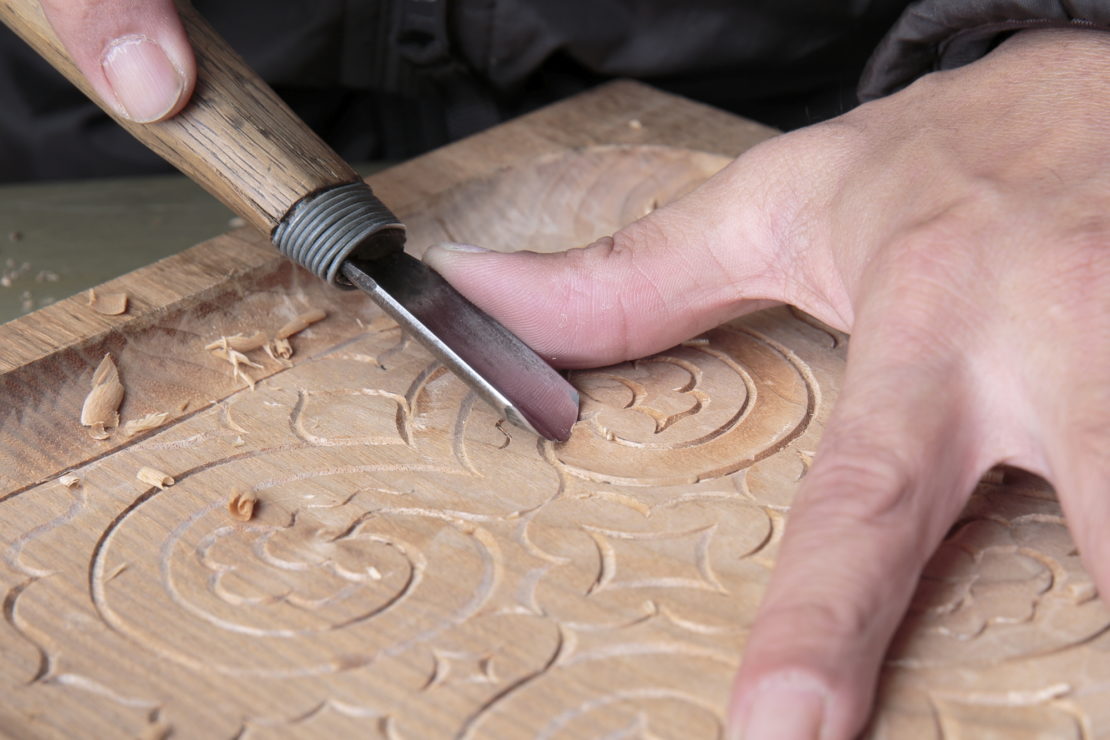
3. Pattern carving
The pattern is designed and the lines traced with a v-shaped gouge.
The carving is then deepened with a rounded gouge to create dimensionality and shading.
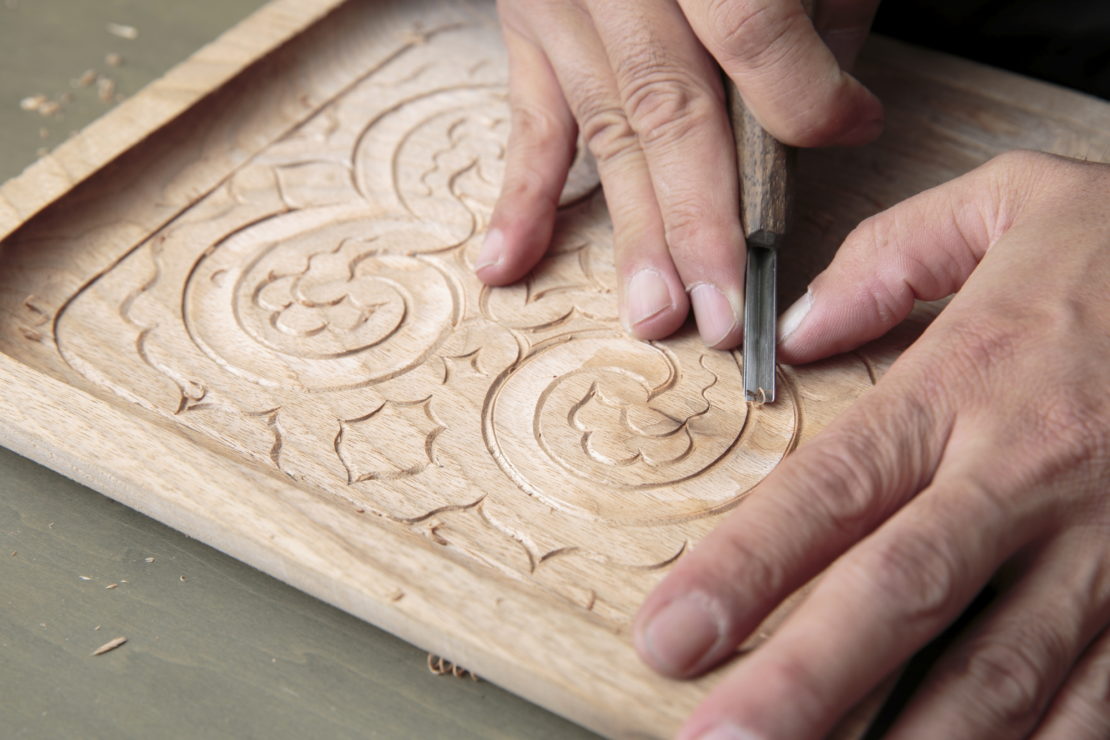
4. Double-line engraving
Adding more lines to the pattern enriches the carving.
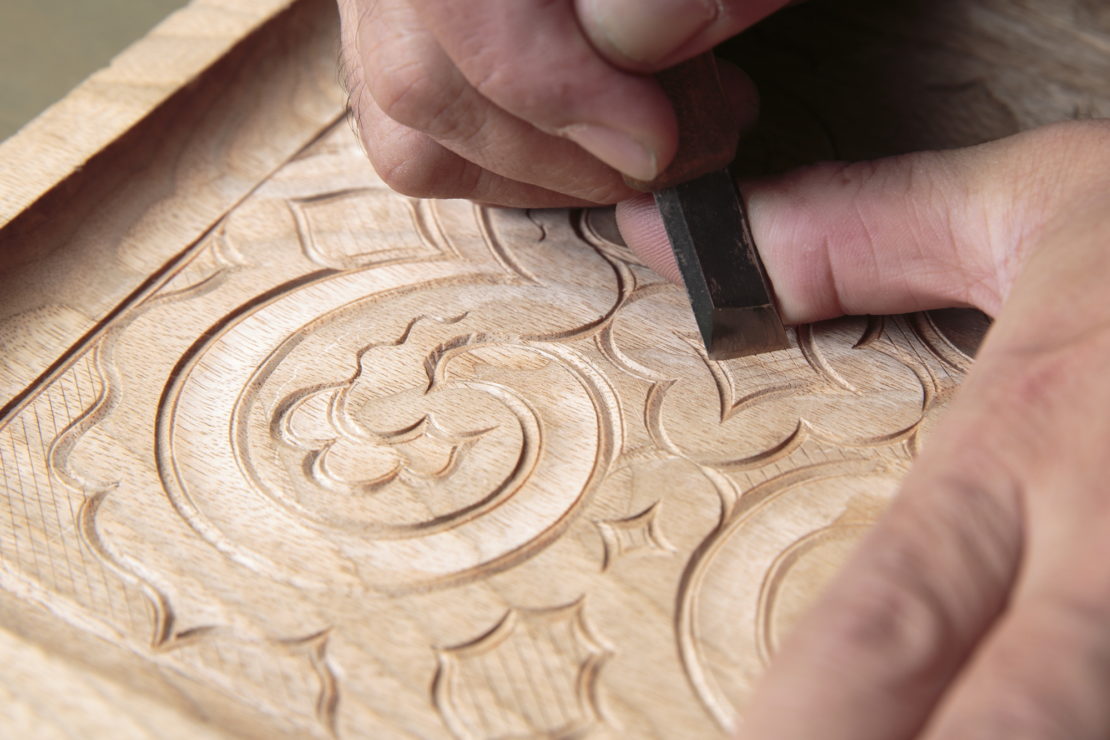
5. Tracing the ramram-noka
The carver uses a seal-carving knife to draw the scale grid lines keeping the woodgrain vertical, filling the spaces between the morew-noka and sik-noka patterns.
Extensive use of this scale pattern is one characteristic of Nibutani Ita.
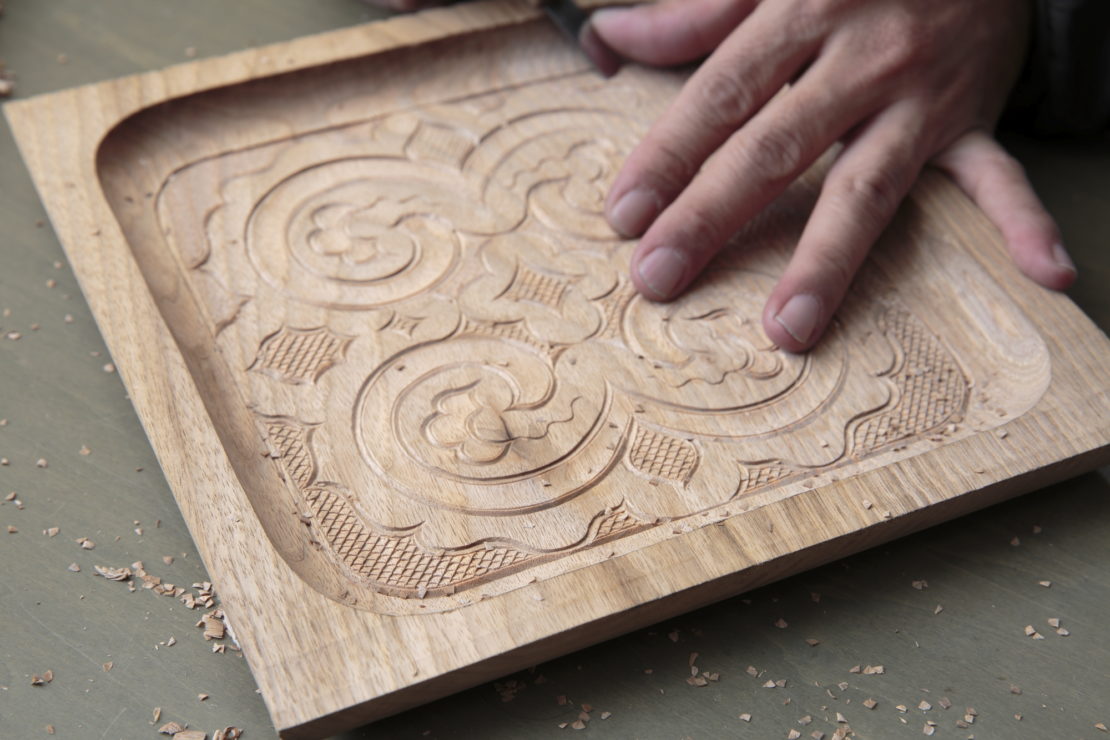
6. Bringing out the ramram-noka
Each scale is worked with the reverse edge of a seal-engraver.
Half of each space is shaved away to better express the size and unique character of the scales.
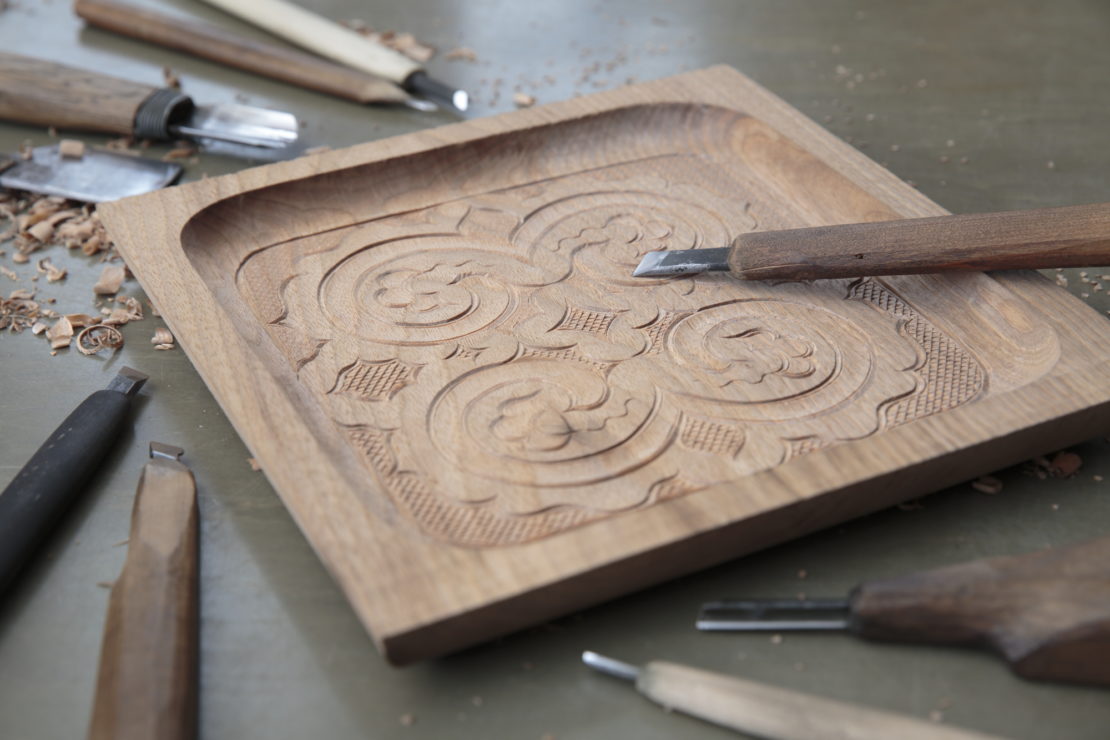
7. Finishing
Minor adjustments finish the carving.